


今年以来,公司深入贯彻落实“用紧日子过好日子”理念,以精益管理为抓手,以技术创新为驱动,在保障生产稳定运行的前提下,深入挖掘降本增效潜力,顺利完成了厂内物料转运系统升级改造项目,通过“减环节、降能耗、控污染”三管齐下,交出了一份环保效益与经济效益双赢的答卷。
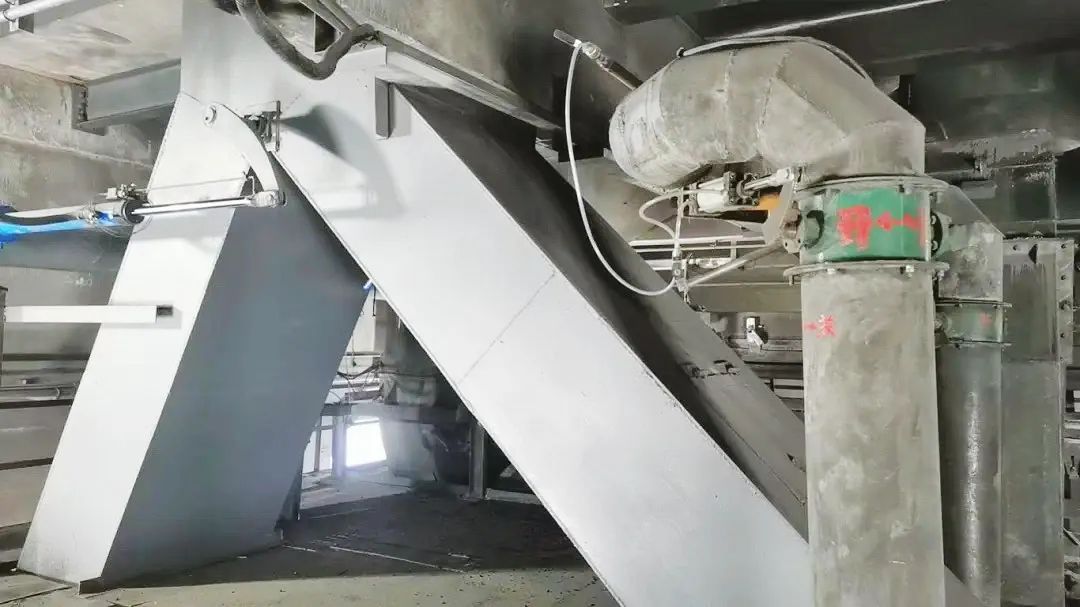
聚焦痛点 精准施策破困局
原转运系统需经转1a——2a——3a三级皮带接力输送物料,流程冗长导致撒料扬尘问题突出,不仅造成物料浪费,更影响环境和职业健康发展。同时设备维护成本较高,皮带清扫作业劳动强度大,动力电消耗升高,成为制约降本增效的“肠梗阻”。公司相关技术人员立足生产实际,以“消除浪费、创造价值”为导向,确立了“简化流程、智能升级、绿色生产”的改造方针。
精简流程 降本增效见真章
改造过程坚持“能用尽用、能修不换”原则,在设备更新中彰显过“紧日子”的智慧。通过拆除冗余的Z2a皮带及附属设施,运输路径缩短30%,系统复杂度降低40%,仅此一项就减少设备维护成本1.8万元/年。公司巧用“修旧利废”策略,将旧皮带架等设备改造再利用,结合楼板开洞部位钢梁加固与混凝土修复,在确保结构安全的前提下,实现改造费用压降25%。
创新驱动 智慧升级提质效
在关键节点增设三通分料器,构建起“一键切换”智能分料系统,使物料输送方向调整后时间缩短至3分钟内,彻底告别传统二次转运模式。配套实施的电气自动化改造,实现了分料器与原有设备的联动控制,电动翻板阀远程联锁控制精度达98%以上。通过在下料口加装密封装置和除尘风管,现场粉尘浓度显著下降,作业环境实现质的飞跃。
绿色发展 效益双收谱新篇
改造后系统年节电量达5万千瓦时,直接节约生产成本2.5万元,物料输送稳定性同比提升15%,设备故障率下降40%。该项目形成的“精简流程+智能改造+绿色升级”技术方案,为同类系统改造提供了可复制范本。经测算,全面推广后预计年可创造综合效益超百万元,真正实现了“改造一个点,优化一条线,激活整个面”。
过紧日子不是降低标准,而是要向管理要效益,向创新要动力。此次改造实践证明,只要把过“紧日子”理念融入生产经营全链条,就能在降本增效的赛道上跑出加速度。未来,公司将持续深化精益管理,让每一分钱都花出最大效益,让每一项改造都创造最优价值,以实际行动谱写高质量发展新篇章。(高家)